S2W Contracting out of Tunkhannock, PA used FasTrac CE815 Epoxy Grout on a recent high-speed gas compressor grouting project with low clearance. CE815 is a revolutionary epoxy machine grout. It features low dust, high bearing area, low exotherm, fast cure, and pumpable with excellent high-flow qualities.
Learn more about CE815 Epoxy Grout here.
The contractor successfully completed a difficult grout installation using CE815 Epoxy Grout on a high-speed gas compressor with < 2” of clearance, surrounded by piping, conduit, and other ancillary equipment. CE815 has exceptional flow and extended working time which makes it the perfect grout for low clearance on large footprint equipment < 2”.
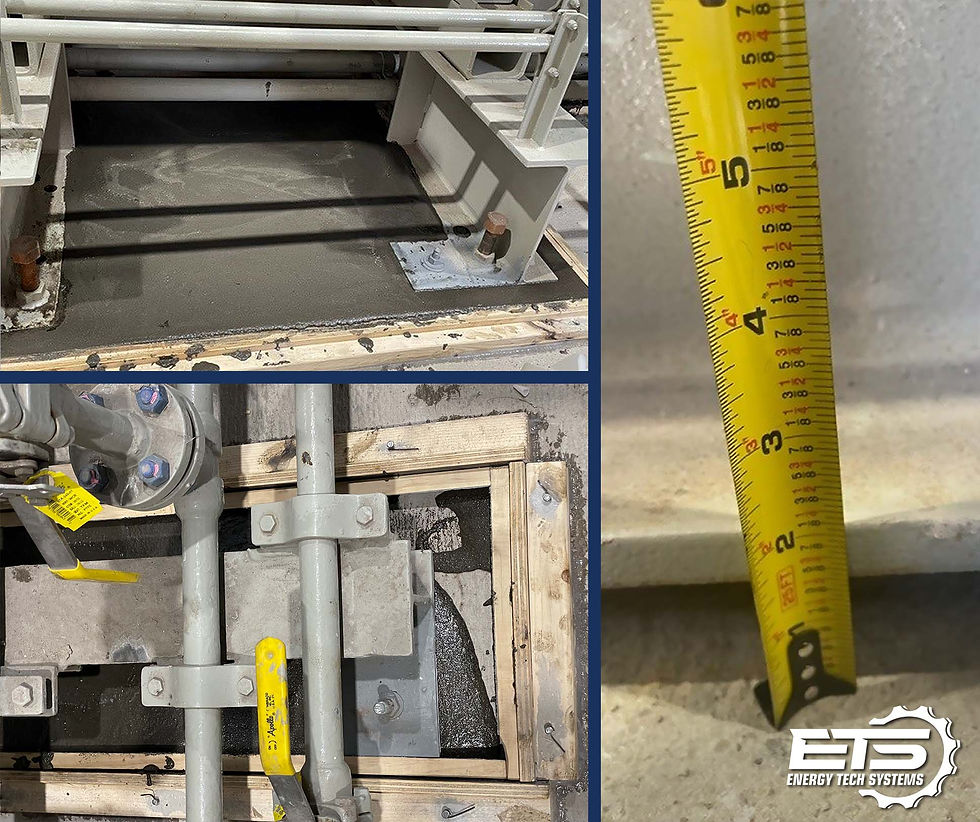
The superior flowability of CE815 requires less head pressure to move. This allowed the contractor to pump the grout at a lower-than-usual volume and keep the grout within the forms and off the conduit, piping, and ancillary equipment. The extended working time at shallow depths of the CE815 allowed the contractor to pump the grout at a lower volume and have sufficient time to finish the exposed surfaces.
With limited clearance, equipment, conduit, and piping obstructing access, a high-flow product is an essential component of a successful grout installation. FasTrac CE815 has superior flow characteristics compared to other epoxy grouts. The CE815 Epoxy Grout aggregate design flows incredibly well without reducing aggregate. Therefore, the contractor was able to use a full 2 cf unit when batching material.
THE DECISION TO USE FASTRAC CE815 EPOXY GROUT FOR LOW-CLEARANCE GROUTING WAS BASED ON DIFFERENT FACTORS:
Application complexity The skid clearance above the top of the concrete was 1.5”-2”. In addition, an intricate array of piping, vessels, and other obstructions made grout placement difficult. The lack of proper access eliminated the option to use headboxes and the low clearance hindered the movement of pump hoses from side to side. The substantial ‘footprint’– large overall dimensions of the skid required an extremely high flow product to flow the width of the skid with minimal positive head pressure.
Construction schedule During the construction phase, grout work was required to be done as quickly as possible to contribute to a faster schedule and a quicker completion date. As a result, CE815 Epoxy Grout was chosen to achieve the shortest turnaround time between grouting operations.
Weather conditions The project location experienced variable weather conditions in early spring. While the installation was inside a building, it lacked heating, so temperatures inside the work areas were more susceptible to outside conditions. For grouting to be successful under these conditions, special preparation, handling, and installation techniques were required.

THE SUCCESSFUL GROUT INSTALLATIONS IS DIRECTLY ATTRIBUTED TO:
A professional grouting contractor who is well prepared with a plan and the proper equipment to complete the job, and understands the conditions, requirements, and selecting the right material needed to pump the grout under the equipment.
Using the pump provided a consistent flow of material and eliminated the use of head boxes and buckets, resulting in time savings, increased efficiency, reduced waste, and lower cleanup times. By decreasing the turnaround time between grouting operations, the contractor was able to complete the grout installation within the scheduled three-day period, resulting in minimal downtime.
AS A RESULT OF SELECTING CE815 FOR THIS INSTALLATION, THE CUSTOMER ENJOYED A NUMBER OF ENHANCED OPERATIONAL AND PERFORMANCE BENEFITS.
CE815 Epoxy Grout does not require reducing aggregate to improve grout flow which reduces the number of units needed and reduces costs.
The superior flowability of CE815 Epoxy Grout was the key to moving grout across the full width and length of the equipment skid.
CE815 Epoxy Grout is an excellent grout to use when pumping.
The 2 cubic foot unit size CE815 Epoxy Grout allows for more productive grout batching and high-output placement with less time and effort.
The CE815 Epoxy Grout’s excellent side-to-side flow with limited head pressure allowed for placement in a low clearance grouting location. The extended working time (>60 minutes) allowed the contractor plenty of time to place the grout and finish the surfaces. The combination of CE815 Epoxy Grout and a professional grouting contractor turned a difficult environment into a routine grouting project.
About FasTrac CE815 Epoxy Grout
FasTrac CE815 Epoxy Grout is a revolutionary, three-component, 100% solids high-performance epoxy machine grout. It is characterized by low dust, high bearing area, low exotherm, negligible shrinkage and creep, fast cure, and pumpable with excellent high flow qualities for improved workability and placement.
CE815 Epoxy Grout is ideal for high-stress applications such as wind turbines, gas transmission, refining, chemical processing, pulp and paper, crane rail, marine, and other machine base plate grouting. New equipment installations or re-grouting applications subject to chemical attack and extreme vibration are ideal for CE815 Epoxy Grout. CE815 can also be used as an anchoring adhesive.
CE815 Features
Made in America
High Impact Resistance
High Early Strength
High Effective Bearing Area
Excellent Flowability
Low Exotherm Cure for Deep Pour Capability
High Oil and Chemical Resistance
Precision Grouting with Negligible Shrinkage and Creep
Pre-Measured Units
Easy Soap and Water Clean Up
Where to Use
Wind Turbines
Gas Transmission
Refining
Chemical Processing
Pulp and Paper
Crane Rail
Marine and Other Machine Base Plate Grouting
New Equipment Installations
Applications Subject to Chemical Attack and Extreme Vibration